ZERO WASTE: SOLVENT To manufacture lithium-ion batteries, a solvent is used to coat RECOVERY SYSTEM metal electrodes inside the cell. During manufacturing, this solvent evaporates and is carried away with warm air, leaving behind powders coated evenly on the metal foil. The solvent vapor is then condensed out of the air, and the used solvent is collected as a waste liquid. In conventional battery factories, this used-solvent liquid is trucked o!site to third-party processing centers. To avoid the high financial and energy costs of this o!site treatment, Tesla designed our own dedicated solvent refining process to convert waste solvent back into reusable solvent in a closed-loop fashion. This solvent refining system was constructed onsite and has been operating since the end of 2017, demonstrating a greater than 95% conversion of waste solvent. This system has also eliminated the need for more than 30 tanker trucks per week that previously would have transported this material to and from an outside refiner. Due to our onsite refining system that was designed specifically for this application, the purity of this refined solvent has shown to be even higher than solvent purchased from third-party suppliers. The solvent refining process is typically very energy intensive, so Tesla developed a custom heat pumping system to minimize total energy consumption. Waste heat that is usually sent to a cooling tower is instead captured as recovered heat. The implementation of this closed- loop steam-water vapor compression heat pump system resulted in an approximately 85% reduction in energy consumption when compared to a standard system. This heat pump system was the first patent application filed for any Gigafactory 1-related operation and was granted by the U.S. Patent and Trademarks Office in November 2017. 30
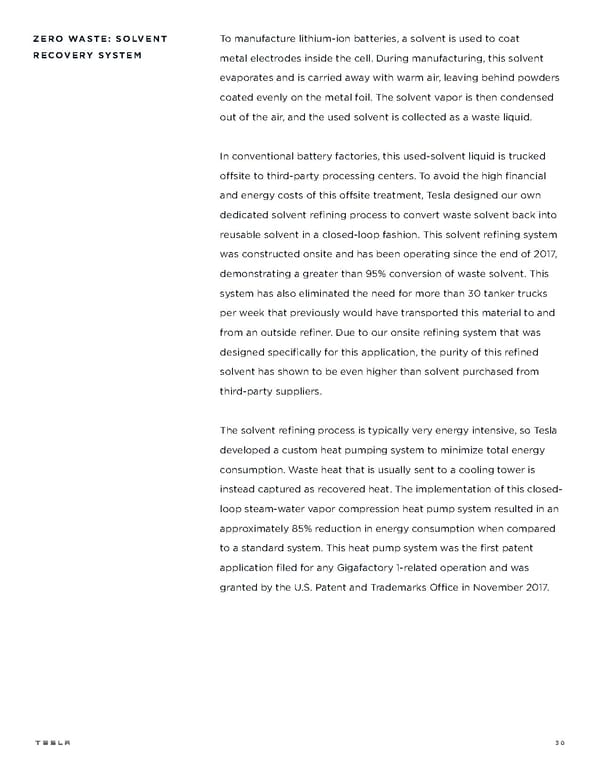