Reducing Carbon Footprint Even Further While emissions from the manufacturing phase can account for a relatively minor portion of lifetime vehicle emissions when Tesla Manufacturing Footprint: compared to the use phase, it is still an important part of lifecycle emissions. These are the steps that we are taking to reduce Current Actions the manufacturing GHG footprint: 1. Building new, better designed, more efficient vehicle factories Building a factory from the ground up with sustainability in mind can have a material impact on reducing energy use. For each component that requires less movement around the factory, and as we use fewer robots in the vehicle production process, energy consumption declines. Our Fremont Factory, where we started operation in 2010, was built over 60 years ago by established automotive original equipment manufacturers (OEM). While substantial improvements have been implemented since, it was not possible to fundamentally change the layout of this facility. In contrast, Tesla’s newer factories are built by us from the ground up and designed to be sustainable and efficient. For example, a delivery truck can back up and offload components at the exact part of the production line where such components are needed—reducing emissions associated with the production process. In our quest for constant improvement, we build each new factory to be better and more sustainably designed than the previous one. While we have already completed substantial improvements at Gigafactory Shanghai, further improvements will continue at Gigafactory Berlin-Brandenburg and Gigafactory Texas. Average Lifecycle Emissions in U.S. (gCO e/mi) 2 Model 3 in Fremont, CA Model 3 in Gigafactory Shanghai 500 400 Impacted by energy- 300 efficient factories 200 100 0 Model 3 Model 3 Model 3 Model 3 Avg. Mid-Size Ridesharing Use Personal Use Ridesharing Use Personal Use Premium ICE (solar charged) (solar charged) (grid charged) (grid charged) Manufacturing Phase Use Phase 17
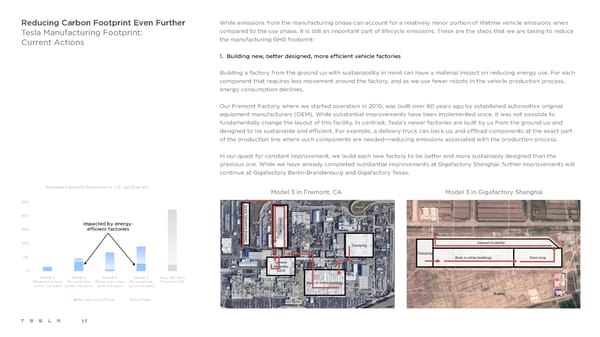