Battery Materials Sourcing On September 22, 2020, Tesla hosted Battery Day where we presented several developments in our cathode technology 2020 Battery Day Highlights roadmap, which are designed to enable the scaling of cathode materials production to TWh/year scale, and in doing so improve the sustainability of our cathode materials. Our novel in-house cathode development aims to reduce resource intensity and the use of hazardous chemicals Tesla will begin in-house production of precursor and cathode materials, leveraging novel processing techniques that we are developing to reduce costs while positively impacting the environmental footprint when compared to the conventional process used in the industry. Tesla’s new cathode process will aim to: • Reduce the energy intensity of the process and the number of process steps; • Eliminate the use of hazardous chemicals, such as sulfuric acid and caustic soda; and • Reduce water consumption by >95%, thereby eliminating a significant waste stream. Our novel in-house process for refining of U.S. lithium resources will reduce carbon emissions and sulfate biproducts We also announced plans to scale in-house lithium refining and the development of U.S. lithium resources in the future. An integrated lithium strategy will enable Tesla to: • Create a domestic U.S. lithium supply chain by sourcing spodumene raw material within the U.S., thereby reducing emissions related to the transportation efforts of moving material from traditional lithium-producing countries in South America and Australia; and • Commercialize a non-standard flow sheet that will eliminate dependence on sulfuric acid and sodium hydroxide, thus removing sulfate biproducts generated during the traditional spodumene conversion process. Our closed-loop production, including in-house recycling, will further reduce carbon emissions in battery manufacturing Finally, our closed-loop cathode production via in-house battery recycling and metals refining will enable us to: • Recover >99% of the metals contained in scrap and end-of-life batteries and convert these metals directly back into cathode materials for re-introduction into our cell production; and • Bypass the extractive processing systems (mining), which significantly reduces the carbon footprint of metals contained in our battery cells. 51
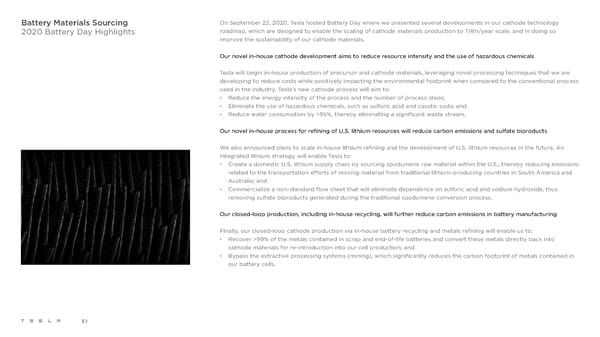