Water Used Per Vehicle Manufactured Future Tesla factories will set a new standard of water use per vehicle Future State Water is becoming increasingly scarce as the climate changes. That is why we are reducing our water usage throughout our operations as much as possible. We have prioritized direct use in manufacturing and will continue to explore the rest of our impact throughout the supply chain and in sales, service and delivery. The “cooling tower makeup” is the single biggest contributor to water usage in any car factory after paint operations. As water that cools machinery evaporates, it needs to be topped up regularly. The total cooling tower makeup could be offset entirely by non-potable sources such as rainwater or wastewater. These are some of the initiatives we are taking at Gigafactory Berlin- Brandenburg and/or Gigafactory Texas in order to reduce water consumption per complete vehicle (including cells). 1. Water intensive process optimization We are constantly looking into reducing water consumption by optimizing or eliminating water intensive production processes across our operations. At Gigafactory Berlin-Brandenburg, we will use hybrid cooling towers, eliminate quench tanks in casting and introduce cascade rinsing systems in the paint shop and battery can wash process for cell manufacturing. 2. Rainwater harvesting and reuse We are planning to capture at least 25% of roof runoff (1 million square feet) to a central underground storage system within Gigafactory Texas. Rainwater will be recycled for use in the cooling of manufacturing equipment. In an average year, such systems should save an estimated 7.5 million gallons of potable city water. 3. Reclaimed water (wastewater reuse) Using local treated wastewater could result in offsetting the entire annual cooling tower makeup water demand with non- drinkable uses. At Gigafactory Texas, this could result in an estimated 40 million gallons of potable city water conserved annually, which equates to the total cooling tower needs for a vehicle production rate of about 250,000 vehicles a year. Reclaimed water is available and under investigation for use at both Gigafactory Texas and Gigafactory Berlin-Brandenburg. 4. In-house cathode production As we stated at our 2020 Battery Day, we are developing a more sustainable method to produce cathode in-house. This new production process will decrease the water needed by current cathode production methods used in the industry by ~95% based on our estimates. We are currently validating this new production process at our pilot production line in Fremont, California, and hope to launch it as soon as practicable. 29
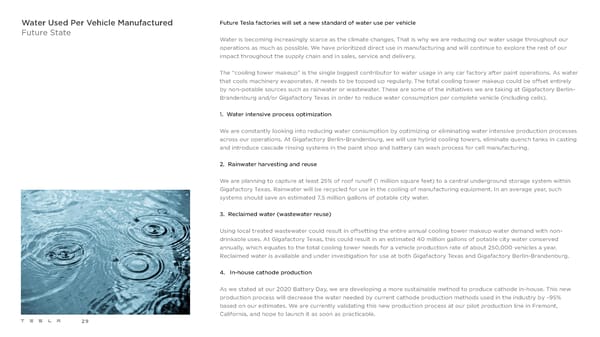